Table of Contents
In this article: Growing industry trends, forecasts and stats about the additive manufacturing industry, today’s achievements and the future of 3D printing.
What should we expect from the 3D printing industry?
Born about 40 years ago, 3D printing opened up a whole bunch of opportunities for creating various models in prototyping, dentistry, small-scale production, customized products, miniatures, sculptures, mock-ups, and much more.
Once people began to use steam engines in factories, then they massively started to use electricity, and later they invented conveyor production. At each of these stages, the production culture made a sharp leap to meet the growing needs of consumers. Nowadays, the factor that gives a new impetus to progress is the spread of digital technologies like 3D modeling, 3D scanning, 3D printing, and robotics, revolutionizing the very perception of the production.
The 3D printing technology
But before we delve into the historical facts, progress, and breakthroughs of technology, let’s define what 3D printing and 3D printers are. Additive technologies (from the word additivity – added) is a layer-by-layer build-up and synthesis of an object using computer 3D technologies. Special hardware – 3D printer is used to build an object in an additive way. This technology is fundamentally different from the traditional methods of manufacturing objects we are familiar with, for example, in milling or cutting, where the object is made by eliminating excess material (the so-called “subtractive production”). First people started talking about 3D printing back in the 80s of the last century. However, this technology began to be widely used only in the early 2010s. Let’s dive into history to understand how it all began and where it is going so rapidly.
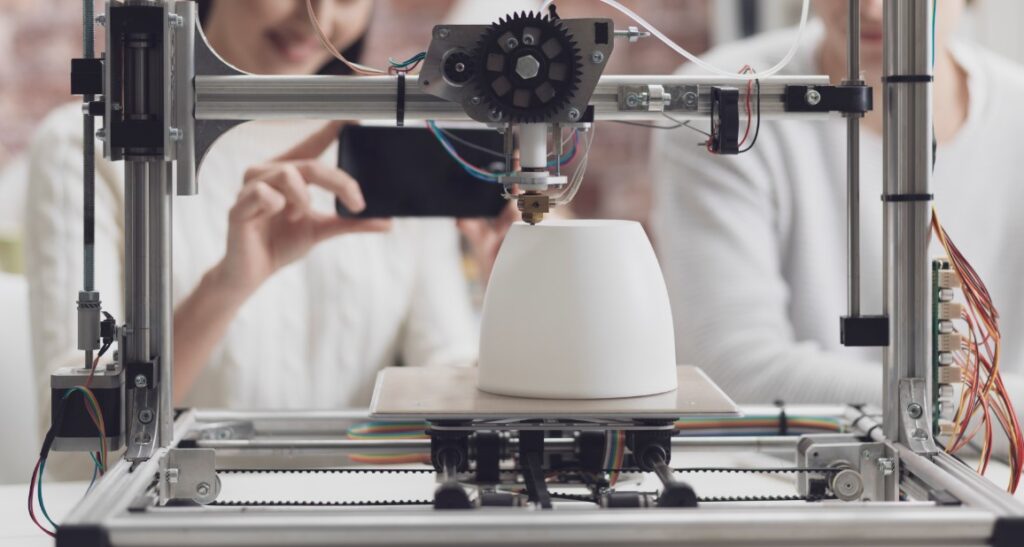
3D printer is used to build an object in an additive way. This technology is fundamentally different from the traditional methods of manufacturing objects we are familiar with. Image by Stokkete, Envato Elements
The emergence of the 3D printing idea
Аll started in Japan. Hideo Kodama, a doctor at the Nagoya City Industrial Research Institute, has applied for a patent for a device that uses UV light to form a rigid photopolymer resin object layer by layer. He was the one who described a modern photopolymer printer. For some reason, he was unable to provide the necessary data for patent registration within a year (1980), as required by patent law, and abandoned the idea. However, in many sources, he is the one called the inventor of 3D printing technology.
At the same time, on the other side of the ocean, an American Chuck Hull worked for a company that specialized in making countertop and furniture coatings using UV lamps. The process of making small plastic parts for prototyping new product designs could take up to two months. To speed up this process Hall decided to combine UV technology and place thin plastic in layers.
Working in a small laboratory on weekends he finely found the way through. As a material, the inventor took acrylic-based photopolymers that harden under the influence of ultraviolet radiation. Finally, after several months of experimentation, he managed to print a sample. As his wife recalls later, Chuck brought home an eyewash cup that looked more like a communion cup. This bowl is officially considered the first-ever 3D printed object and is still kept by the Hull family: after their death, it will pass to the Smithsonian Research Institute in Washington.
The first patent in 3D printing and further developments
In 1984, Chuck Hull filed a patent application, which was approved two years later under the name “Apparatus for creating three-dimensional objects using stereolithography.” Later, Hall founded a company of his own, and in 1988 released the first commercial 3D printer, known as the SL1 model. Around the same time, another method of 3D printing appeared which was SLA printing.
This is selective laser sintering (SLS), which uses a laser to turn a free-flowing powder (instead of resin) into a solid material. The innovation was carried out by Dr. Professor Joe Beeman and his student Carl Deckard at the University of Texas at Austin. Remarkably, the author of the idea was none other than Karl. Later, in 1987, the professor and his student, founded Desk Top Manufacturing (DTM) Corp. In 2001, the company was united with Hull’s 3D Systems.
In parallel with these developments (or a little later, in 1988), another simpler and cheaper 3D printing method appeared – FDM (Fused Deposition Modeling), authored by aeronautical engineer Scott Crump. The idea came to him when he was looking for an easy way to make a toy frog for his daughter and used a hot glue gun to melt the plastic and pour it into layers. After successful experiments, the idea of FDM 3D printing was born, which uses the technology of layer-by-layer deposition of plastic filament. Of course, the idea was patented, and Kramp and his wife Lisa Kramp founded Stratasys in 1989. In 1992 the company launched the Stratasys 3D Modeler – its first serial product.
Phase 2 – the era of accessibility
In the distant 90s, 3D Systems, and Stratasys created bulky and expensive units, the cost of which could exceed hundreds of thousands of dollars: only big corporations and companies in the automotive and aerospace industries could afford their production. Moreover, these printers had a lot of limitations and could not be widely used, which slowed down the technology’s development. The turning point for the popularization and availability of 3D printers came 20 years later in 2005, with the RepRap project (Replicating Rapid Prototyper) – а self-replicating mechanism for rapid prototyping.
Dr. Adrian Bauer was one of the main enthusiasts of this mechanism. The “self-copy” mechanism was the main idea behind this project. So, a group of enthusiasts led by Adrian was finally able to create a 3D printer on a budget for home or office use. The idea quickly found its way into the hands of three New York City technologists who started a desktop FDM printer company, MakerBot. The second turning point in the modern history of 3D printing was in full swing.
As part of this phase, a technology like bioprinting was developed. Thomas Boland of Clemson University has patented the use of inkjet printing to 3D print living cells, making it possible to print human organs in the future. Dozens of companies around the world conduct research in this area. An important application of this technology is the technology of creating prostheses, first conventional, and then bionic. In 2008, the first printed prosthesis was successfully transplanted into a patient and allowed him to return to a normal lifestyle. An important step in the development of technology was open source print files’ availability on the Internet. Websites www.thingiverse.com, www.myminifactory.com, and many others provide both free and paid files for 3D printing.
Phase 3 – 3D printing today
The technology that was affordable only for big enterprises more than 30 years ago is now available to the mass consumer. Moreover, 3D-printers prices have dropped drastically, becoming more user-friendly. The number of users grew, due to the huge community of enthusiasts who were ready to help beginners. The technology development vector leaped with the availability of software and ready files for creating 3D printed models. Using photopolymer 3D printers made it possible to print detailed models with high precision and resolution.
3D printing started becoming a standard solution in industries such as dentistry, jewelry, and orthopedics, in other industries, the implementation is in full swing. The opportunities are endless – from building houses to neurosurgery, from chocolate printing to metal printing.
From History to Numbers: 3D Printer Market Statistics and much more
After a historical overview, let’s talk about numbers, trends, and the future in general, because 3D printing, since its inception, has been and remains the technology of the future. To begin with, the 3D printing market is segmented by printer type (desktop and industrial), technology (stereolithography, deposition modeling, selective laser sintering, electron beam melting, and digital light processing), material type (metal, plastic, and ceramic), end-user industry (Automotive, Aerospace & Defense, Healthcare, Construction & Architecture, Energy & Food), and Geography.
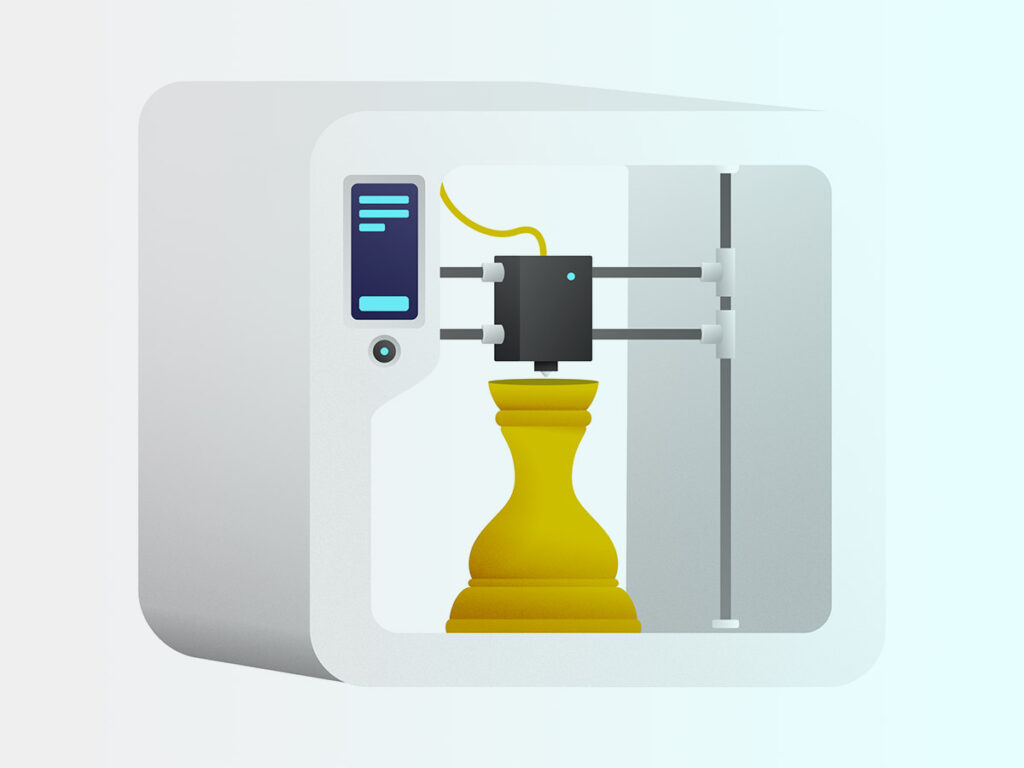
The 3D printing market was valued at 12.6 billion in 2021 and is expected to reach 34.8 billion by 2026
According to ReportLinker, the 3D printing market was valued at 12.6 billion in 2021 and is expected to reach 34.8 billion by 2026, at a CAGR of 22.5% over the forecasted period (2021-2026). Experts note that North America will account for 34% of growth, and one of the key drivers of growth will be the increasing demand for products that can be personalized by 3D printing technology. In addition, the growth of the additive manufacturing market is expected to be driven by the growing demand for new materials. Moreover, users are showing great interest in personalized products. Therefore, they either order such products from manufacturers or buy desktop 3D printers to design and 3D print products themselves. As desktop 3D printers become more affordable, consumers are willing to buy them to print toys and home decor items. Analysts included 3D Systems, EOS GmbH Electro Optical Systems, HP, Materialize NV, and Proto Labs in the top five of the most influential participants in the 3D printer market.
Additive manufacturing as Industry 4.0 driver
Today, nine drivers have been identified that have a major impact on the development of Industry 4.0, including additive manufacturing. As one of the engines of Industry 4.0, additive manufacturing also requires significant qualitative and quantitative changes, but first of all, it needs to be integrated into fully-automated production.
Large aviation, automotive, defense, instrument-making enterprises, medicine, including dentistry, education, and many others have already appreciated the benefits of using 3D printing and are actively integrating it into their workflows. The most successful companies have even adopted internal standards for the use of additive technologies and materials. Remarkably, internal and external logistics occupy 95% of the production cycle, while traditional machining processes are less than 5%, and additive technologies are excellent in that they significantly reduce the time of logistics operations.
It is expected that digital production will replace some types of mass production in the next 20 years, especially those with a high final cost of production. According to the concept of “Industry 4.0”, the production of the future will not have a large range of equipment. They will be produced on flexible production elements as part of cyber-physical systems Cells and systems will be adapted to a specific order by reprogramming, changing production modules, equipment, tools, materials, and redirecting logistics flows – and all this will happen as soon as possible. Such production centers will be built through complete technical and technological cloning, located near the main points of consumption of products. As a starting point for the implementation of the concept of digital additive systems, one can take the flexible manufacturing systems (FMS) used over the past 30-40 years.
Producing our 3D future: 3D printed world
One of the leading online publications in additive manufacturing – the 3D Printing Industry, conducted a survey among researchers, senior executives, technical experts, and investors to share their vision of the future of 3D printing. Based on this survey, the message was clear: the potential of 3D printing in various fields, including aerospace, automotive, and medicine, is still growing. Some of the latest innovations and breakthroughs in 3D printing are presented below.
Healthcare
The production of bionic prostheses, individual splints, and orthoses is a little part of the application. New 3D technologies are also used in dentistry, maxillofacial surgery, and orthodontics. But the most anticipated application of 3D printing, of course, is bioprinting. Soon, bioprinting will enable to fully restore damaged or lost tissues and organs.
Today more than 100 companies worldwide produce bioprinters for 3D printing. 39% of them are in the USA, 35% are in Europe (of which more than half are in France and Germany), 17% are in Asia, and 5% are in Latin America. Moreover, the most promising direction in bioprinting is the 3D-printed skin. It is expected that in five years the procedure will be done directly on a person, on top of or instead of the damaged area. More complex organs, such as kidneys or leavers, have so far only been printed as prototypes or transplanted into mice, not humans. Software for bioprinters is also at the development stage: to bring it to perfection, it is necessary to process a large amount of medical, clinical, and statistical data.
Generative design
Today, the cost of 3D printing and the price of 3D printers have already dropped to a level that allows us to think about industrial production based on them. As for the opportunities of the “generative design – additive technologies” tandem, they are at a level several analysts call nothing more than another industrial revolution and which will definitely impact the future of the 3D printing industry.
Generative design is fundamentally new design technology. It is based on independently generated 3D models without the participation of a designer. In fact, in the “man-machine” system, creative functions are transferred to the computer, and it does an excellent job with them. The reason for beginning using it in CAD is the growth of computing power and the extremely rapid development of 3D printing, a technology that is fully capable of producing parts and objects designed with a new tool.
Criminal justice
Additive manufacturing is used not only in engineering, design, and medicine but also in criminal justice. So in the United States, a case was registered when 3D printing was used to obtain a copy of the finger of a deceased man. While searching for the killer, the police felt that access to his phone was the missing link in the investigation. Michigan State University’s computer science department was able to reconstruct the deceased’s hand and successfully replicate the person’s finger.
The latest breakthroughs in 3D printing and modeling industries
microArch
Miniaturization is the next frontier for 3D printing. Recently, BMF launched the microArch S230 additive machine based on Projection Micro Stereolithography technology, which allows producing functional products with a resolution of up to two microns. The microArch S230 is an evolution of the microArch S130 with a larger build area of up to 50x50x50mm and five times faster 3D printing. The main advantage of projection micro stereolithography technology (Projection Micro Stereolithography or PμSL) is its high resolution, reaching only two microns and allowing printing of small-sized products with a high degree of detail and minimal tolerances.
This 3D printer features an automatic calibration system and the ability to 3D print materials with higher molecular weights and viscosities up to 20,000 cps, enabling the production of stronger functional parts. The system is compatible with a growing range of engineering and ceramic photopolymers suitable for prototyping and final products.
Raise3D MetalFuse
Raise3D MetalFuse is one of the latest 3D printing systems producing various types of metal parts. It differs from other similar systems on the market in that process of metal printing here is safe, as the filament is used as a consumable, which makes the whole process safe and simple. Compared to other renowned printers on the market, the Raise3D MetalFuse differs from the dangerous and difficult handling of metal powder-based solution materials.
Jet Fusion 4200
Jet Fusion 4200 operates based on “HP Multi Jet Fusion technology”, which is a modified SLS (Selective Laser Sintering): layers of special powder are poured layer by layer, and the desired areas of the layer are selectively sintered under special lighting. The HP Jet Fusion 3D 4200 prints in a fully enclosed temperature-controlled chamber. An infrared lamp/heater passes over the surface selectively fusing the powder to the underlying layer. The completed layers are then dropped to make room for the next one, and so on.
Beegraphy
BeeGraphy is the first-ever “Parametric modeling art hub”, which provides unique innovative tools for 3D and CAD designers, manufacturers, etc. In fact, this platform is the first in 3D printing that can serve as a “quick helper”, allowing you to quickly create prototypes, change their settings, and immediately experiment with 3D printers. This is the advantage of algorithmic modeling, in addition to the fact that the software works entirely online and allows real-time collaboration with partners within a single parametric design project.
Parametric models created with BeeGraphy Editor software are stored on the BeeGraphy platform. Moreover, thousands or even millions of variations out of one generated model are created through parametric changes, which is the best aspect of parametric/algorithmic modeling in the 3D modeling industry.
Construction of homes with a 3D printer
In the field of 3D printed construction, only a few projects have been implemented. Two of them are constructed in Dubai and impressed with their innovative approach and speed of execution. Dubai Municipality office building was designed by Apis Cor, a company that makes 3D printing robots.
This building is the world’s largest 3D printed private building, 9.5 meters high and 640 m2 in area. As for the Office of the Future, which currently houses the temporary headquarters of the Dubai Future Foundation, its elements were printed in 17 days, and the building itself was assembled in 48 hours.
The vision of the future
3D printing is an extremely promising technology that can change the way many things are made. Technology has very great prospects in various areas of industry and human life, which will replace the hard work of people, and print cheaper products with consistently high quality.
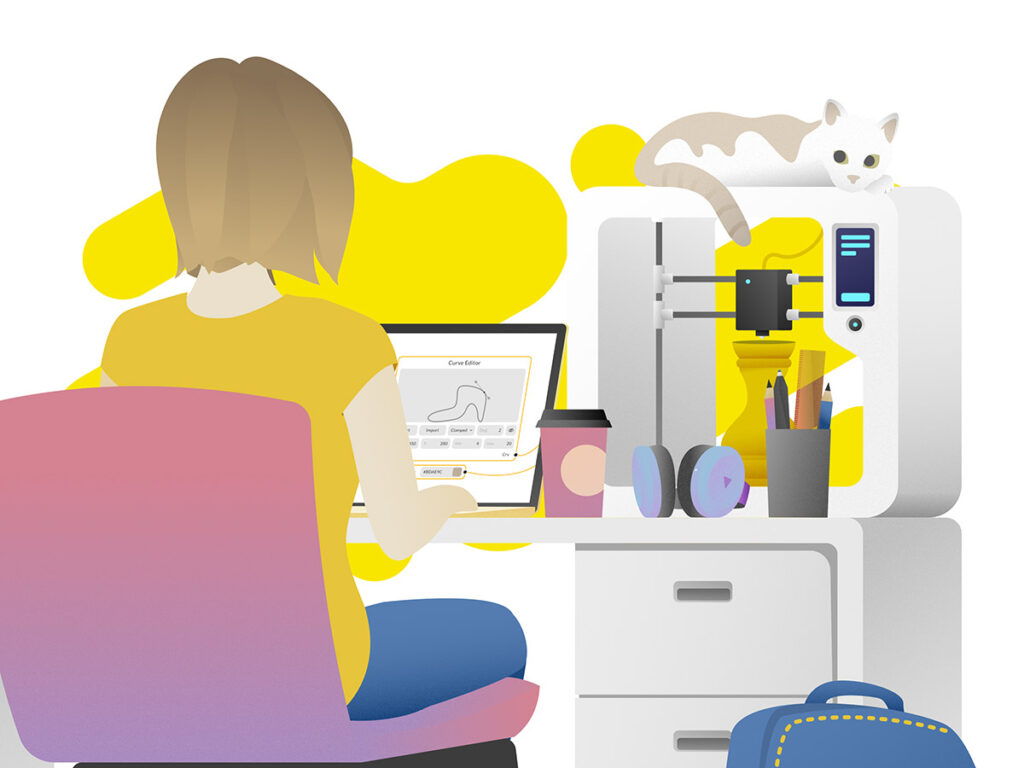
3D printing is an extremely promising technology that can change the way many things are made.
Arno G. Held, Managing Partner, AT Ventures
“In the next 10 years, additive manufacturing will support the transition to a sustainable and resource-efficient civilization. The main applications are in the design and manufacture of lightweight structural components or electric motors.”
Dr. Jeffrey Graves, President, and CEO, 3D Systems
“I hope customization will become a trend not just in the upcoming year but in the next decade. In the nearest future, ML will be a key player in facilitating the integration of AT into existing workflows. Also, I expect to see how AT will drive significant breakthroughs in medicine. AT has already drastically impacted healthcare with unique solutions for surgical planning and medical device design, and I am very excited about the next frontier in healthcare, where bioprinting plays an important role.”
Avi Reichental, co-founder and CEO of Nexa3D
“AT will play a key role in reversing global warming by reducing weight, reducing its carbon footprint, localizing production, reducing energy consumption and reducing waste, and shifting to plant-based materials. Over the next decade, AT will become a cost-effective tool for all stages of building an object, from concept models to aftermarket parts and everything in between. The technology will level up becoming a must-have tool to produce aircraft, trains, cars, and houses, as well as for the creation of atomic structures. A stage of “replicator” gradually becomes closer, especially in the field of bioprinting.”